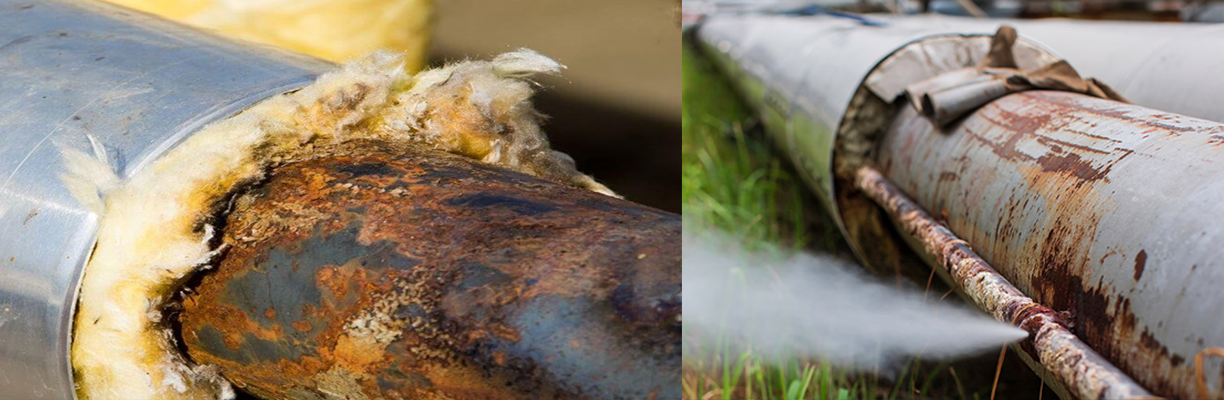
Corrosion Under Insulation (CUI)
Kosteuden kertyminen voi johtua useista syistä. Mikäli CUI:tä ei havaita ajoissa, saattaa se johtaa odottamattomiin pysähdyksiin osassa laitosta tai jopa koko laitoksen pysäytykseen. Harvinaisissa tapauksissa CUI voi johtaa myös tapaturmaan.
World Corrosion Organization arvioi, että korroosioon liittyvät vauriot öljyn ja kaasun jalostuksessa aiheuttavat uskomattomat 1,7 miljardin kustannukset vuosittain.
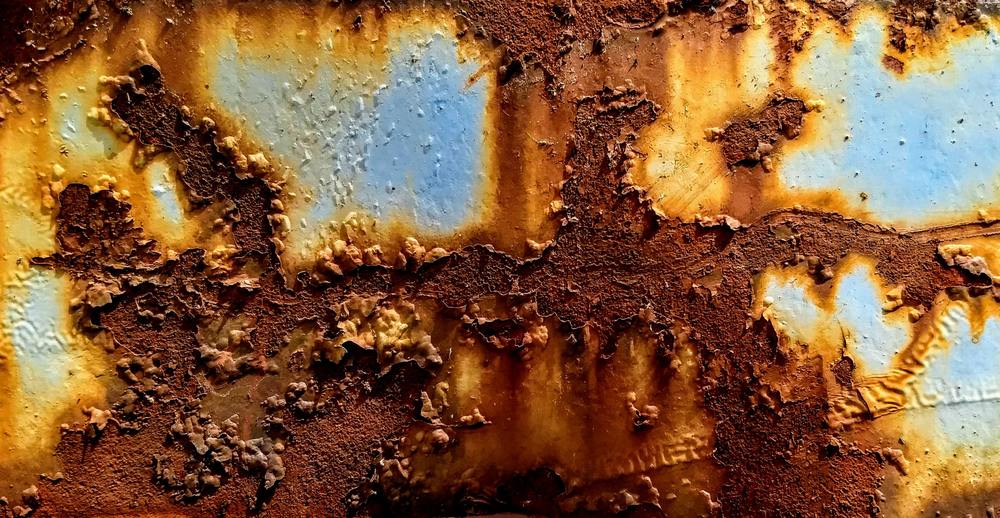
Korroosio eristyksen alla on piilevä ilmiö. Käytännön syistä ei aina pystytä käyttämään parhaimpia eristemateriaaleja tai suorittaa soveltuvimpia tarkastusmenetelmiä.
Tunkeutuva vesi on suurin CUI:ta aiheuttava ongelma. Korroosio voi vahingoittaa vaippaa, eristemateriaalia tai alla olevia putkia tai laitteita. Korroosiota voi esiintyä yhdessä useista eri tyypeistä, kuten kloridi-, galvaaninen, hapan tai emäksinen korroosio.
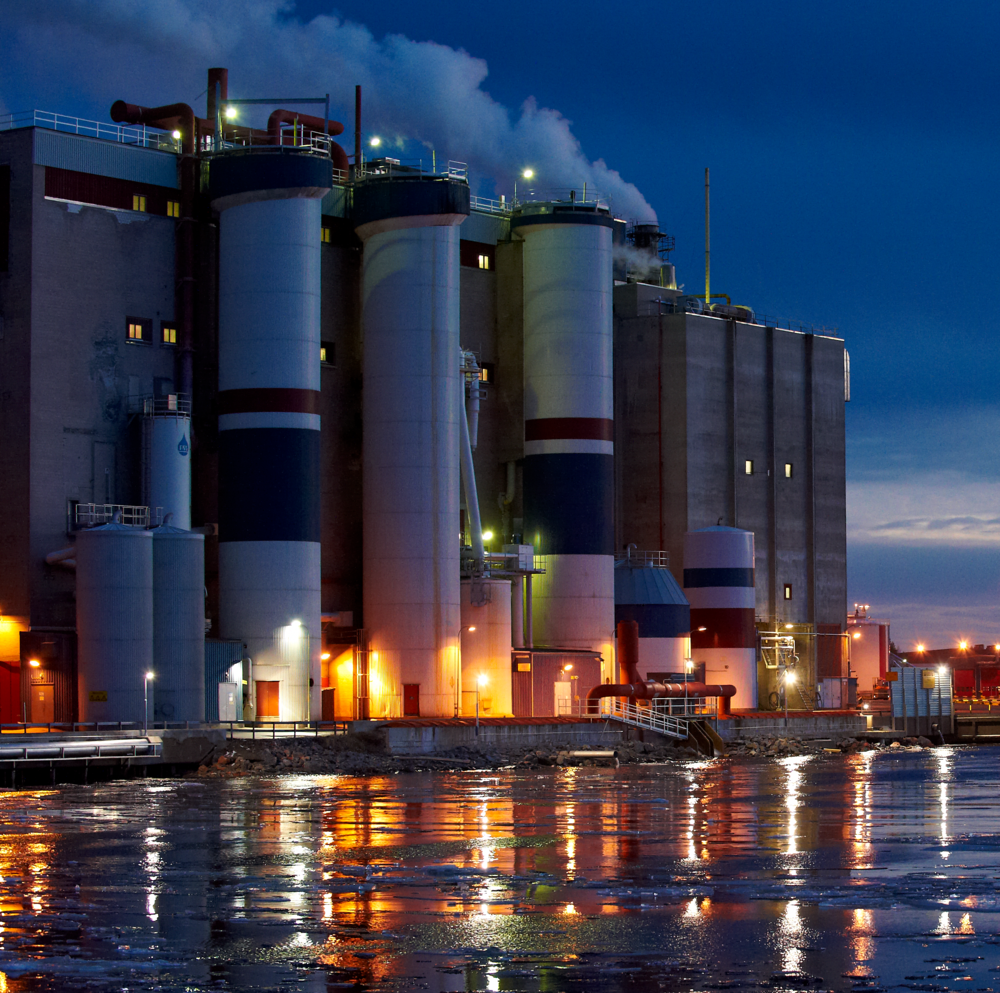
Ympäristöolosuhteet, jotka saattaa johtaa korroosioon eristeen alla
CUI-kustannusten ennustaminen on vaikeaa - ne voivat olla hyvin paikallisia tai jokseenkin yleisiä. Alla on lueteltu muutamia ympäristöolosuhteita, jotka johtavat korkeampiin CUI-määriin:
- Meriympäristöt sekä kuumat tai kosteat ympäristöt
- Sateinen ilmasto
- Vuoto höyrysulussa
- Vaihtelevat olosuhteet
- Eristeestä tai ilmakehästä vapautuvat vesiliukoiset epäpuhtaudet (esim. kloridit ja sulfidit)
- Järjestelmät, joiden normaali toiminta on tyypillisesti ilmakehän kastepisteen alapuolella
- Kosteutta sitovat eriste materiaalit
CUI on uhka monilla toimialoilla. Jos se jätetään huomioimatta, jää se piiloon eristeen alle ja saattaa näyttäytyä vasta vakavina vikoina.
CUI syntyy veden tai kosteuden tunkeutumisesta eristeen sisään sekä kondensaation saastumisen seurauksena. CUI:ta voi myös syntyä ulkoisista lähteistä (esim. sade, sprinklerijärjestelmät).
CUI voi olla hyvin paikallista, ja suurin osa laitteista ja putkistoista voi siitä huolimatta olla hyvässä kunnossa.
Tästä syystä pistokokeilla ei välttämättä löydetä kaikkia altistuneita kohtia.
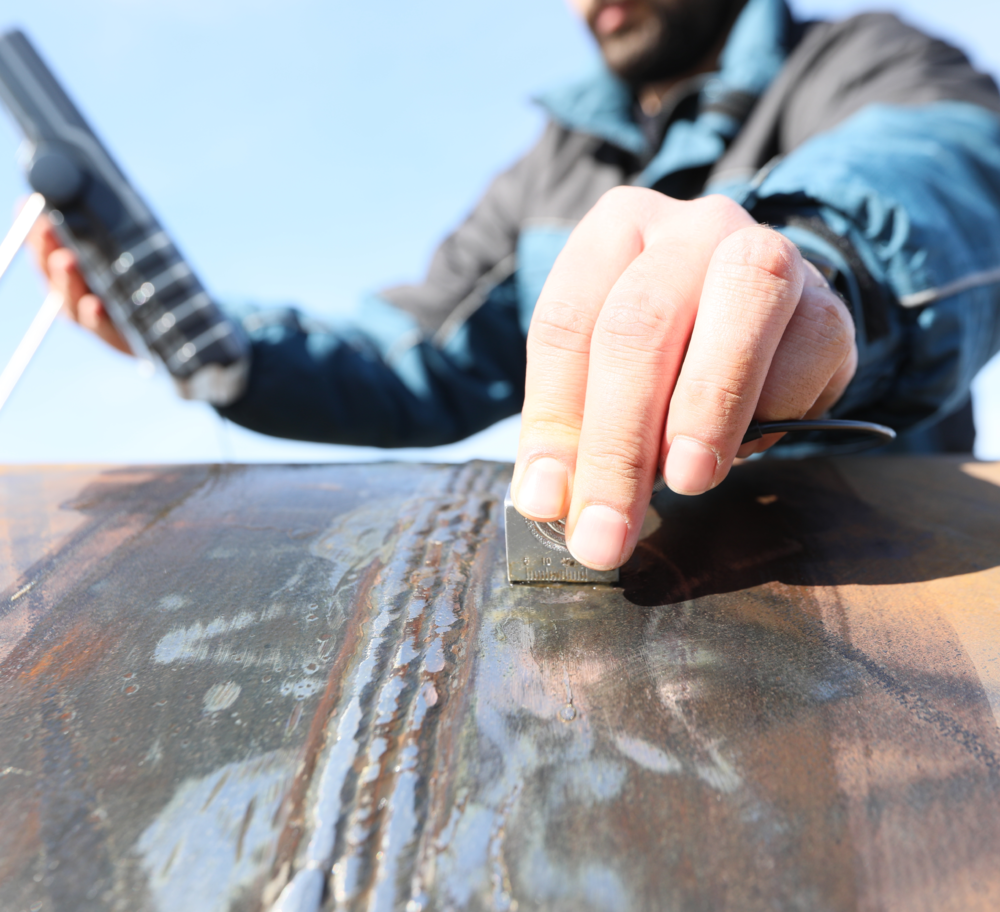
Neljä tähän mennessä tunnettua testausmenetelmää sisältävät kaikki jonkinlaisen rajoitteen
1. Pulssivirran pyörretestaus
Pulssivirtapyörrtettä (Eddy Current) voidaan käyttää CUI:n havaitsemiseksi ja sillä voidaan suorittaa tarkastukset eristelevyille (tietyt materiaalit: GI-, SS- ja Al). Eristeen paksuus voi olla jopa 300 mm ja metallin paksuus jopa 100 mm. Edistyksellinen menetelmä, pulssivirtapyörrematriisi, on erittäin nopea. Tämän tekniikan rajoituksena on lukeman tarkkuus, joka voi vaihdella 10 %, mutta tärkein etu on, että se voidaan suorittaa putkien ollessa vielä toiminnassa.
2. Ultraäänitestaus pitkällä kantamalla
Pitkän kantaman ultraäänitestaus voidaan suorittaa putkille, joiden halkaisija on vähintään kaksi tuumaa. Tämä vaatii eristeiden osittaista purkua jotta instrumentin kaulus saadaan kiinnitettyä. Ultraääniaallot pystyvät havaitsemaan korroosion putkissa noin 5-200 metrin etäisyydeltä kauluksesta. Havaitsemis etäisyys riippuu esim. pinnoitteesta, korroosion tyypistä sekä putken sijainnista. Tämä järjestelmä pystyy havaitsemaan korroosion yli 3 %:lla poikkileikkauspinta-alasta.
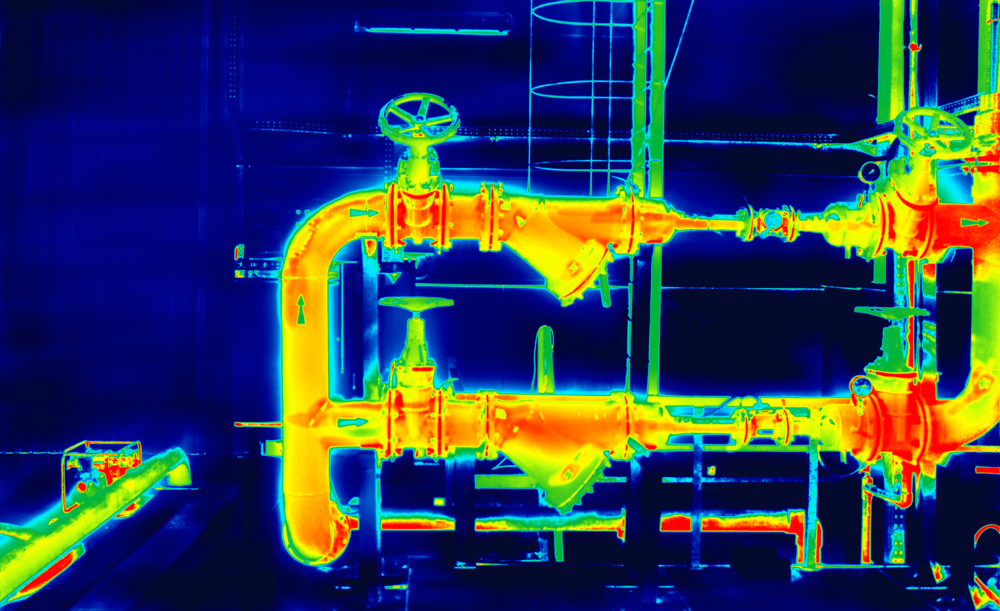
3. Arvioitu röntgenkuvaus
Tietokonetomografiatutkimus voidaan tehdä putkien mutkille korroosion tai eroosion tarkistamiseksi. On olemassa tarkka järjestelmä, mutta jokaisen mutkan testaamiseen kuluu paljon aikaa radiografian käytön vuoksi.
4. Infrapuna termografia
Infrapuna termografia voi olla erittäin hyödyllinen kosteuden löytämisessä eristeen alta, mikä puolestaan voi auttaa löytämään CUI:n. Tämän tekniikan haittapuoli on ilmeinen kuvattaessa kiiltävää eristelevyä. Heijastuksesta tulee liian voimakas ja kameran on silloin vaikea havaita lämpötilaeroja.
Lähde: www.corrosionpedia.com
Viides menetelmä (ainutlaatuinen lajissaan)
Mikä menetelmä on ja mikä on menetelmän etu neljään muuhun menetelmään verrattuna?
Malux CUI Management System, lyhennettynä MCMS, perustuu vakiintuneeseen kosteusanturitekniikkaan, mutta täysin uudella tavalla. Anturi reagoi välittömästi ja voi tallentaa tietoja jopa viikon ajan ennen datapaketin lähettämistä pilveen.
Järjestelmä on langaton ja tällä hetkellä ainoa maailmassa, joka lähettää tietoa IoT-alustalle 4G/5G-verkon kautta CUI:n valvontaa varten. Järjestelmään on upotettu useita turvallisuusominaisuuksia, jossa viestintä on salattu viimeisintä tekniikkaa käyttäen. Anturi on sertifioitu ATEX- ja IECEx-alueelle 0 sekä kaasuryhmälle IIC, joten se sopii useimpiin Ex-luokiteltuihin tiloihin. Yksinkertaisempaa kokonaisuutta ei tällä hetkellä ole markkinoilla saatavilla. Datan lähettäminen pilveen kestää 7–10 minuuttia per anturi, jonka jälkeen käyttäjä saa tiedon näytölleen. Nykypäivän langalliset järjestelmät (esim. verkkokaapeli) edellyttävät, että eristys poistetaan ennen asennusta ja lähetys vaatii porttikäytävän luokiteltuihin tiloihin, mikä tarkoittaa monia kalliita Ex d -laatikoita kentällä, mikäli haluat saada kattavan valvonnan järjestelmästä. Kaikki tämä vältetään MCMS:llä.
Hyödyt verrattuna nykypäivän langattomiin järjestelmiin?
Nykyiset langattomat järjestelmät käyttävät Bluetoothia, Wireless HARTia tai Wifiä, jotka edellyttävät laajaa tukiasemaverkkoa. Näissä järjestelmissä on samat ongelmat kuin langallisissa. –Kentällä useita Ex d -laatikoita signaalin sieppaamiseksi ja lähettämiseksi. Tätä ongelmaa ei MCMS-järjestelmässämme ole.

Miten MCMS-järjestelmä toimii?
Näin se on rakennettu
Konsepti perustuu 3 osaan. Tieto on arvo, jonka järjestelmä toimittaa.
- Miltä tilanne eristeiden alla oikeasti näyttää?
- Missä riskimme sijaitsee?
- Kuinka voimme välttää suunnittelemattomia huoltokatkoja?
- Voiko CUI aiheuttaa palavan kaasun/nesteen vuotamisen putken läpi, joka lopulta syttyy?
Käyttäjänä saat selkeän kuvan siitä, miltä tilanne näyttää putkien eristyslevyn alla. Näiden tietojen avulla voidaan tehdä oikeita päätöksiä ja siten säästää rahaa.
Näin se on rakennettu
1. Tietojen kerääminen
Fusion 310 CUI mittaa jopa 12 kertaa päivässä. Se on redundantti kahden anturinsa ansiosta ja se mittaa suhteellista kosteutta (RHt), vettä ja lämpötilaa. Anturi lähettää tiedot langattomasti 4G/5G-verkon kautta pilveen, sisäänrakennetun E-sim-kortin avulla.
2. Toiminnot
Tiedot kerätään, analysoidaan ja tallennetaan pilveen, jossa käyttäjä hallinnoi järjestelmää. Täällä tapahtuu laitteen tunnistaminen, valvonta, tietojen kirjaaminen ja hälytystasojen asettaminen. Järjestelmän laajentamisen (antureiden asennus/lisäys) yhteydessä käyttäjä / ylläpitäjä hoitaa kaiken täältä.
3. Visualisointi
Avain on siinä, kuinka IoT-alusta on koodattu (machine learning) anturien toimittaman tiedon analysoimiseksi ja siinä kuinka havainnollistamme sen käyttäjälle. Tämä on järjestelmän tarkoitus.
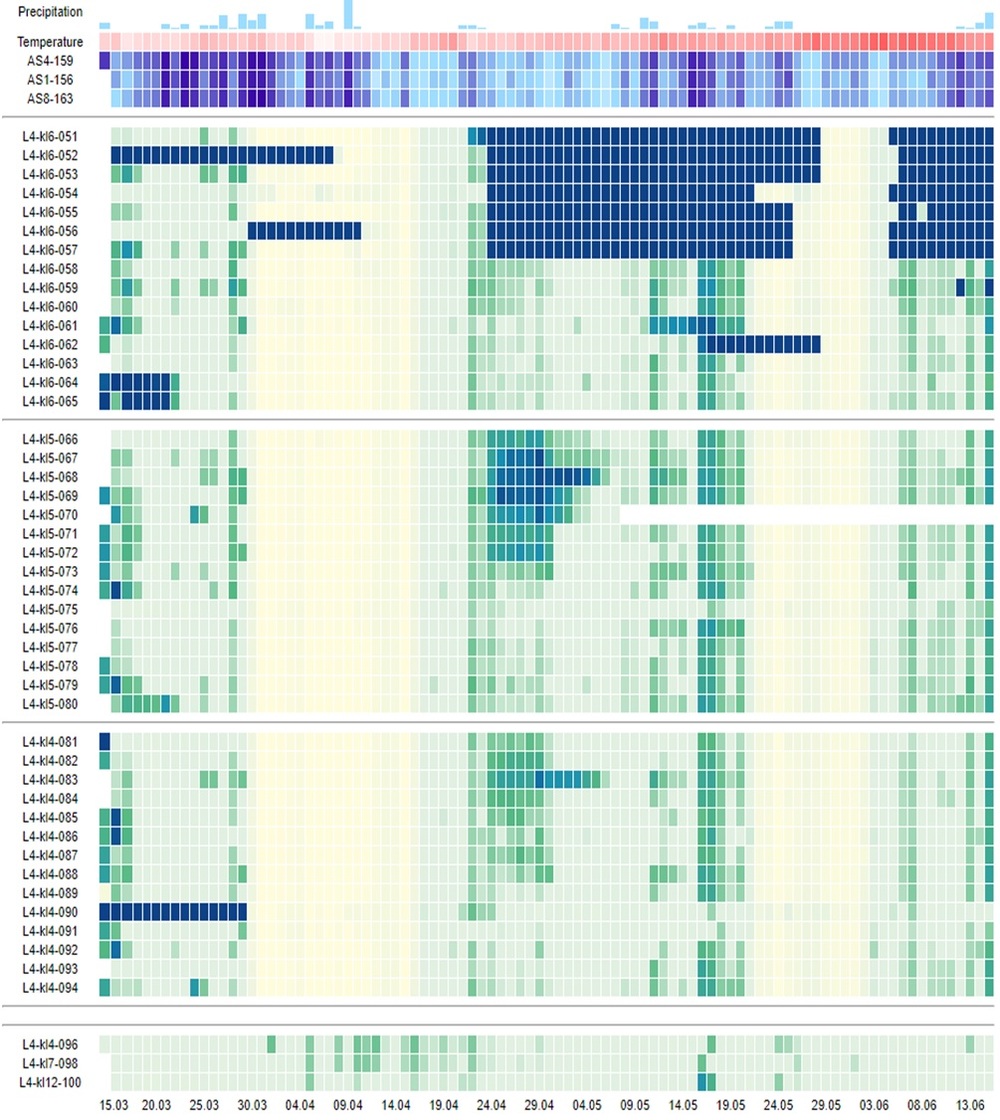
Water Presence -kartallamme (WAP) tilanne visualisoidaan selkeällä tavalla.
Ajatuksena on, että MCMS antaa käyttäjälle selkeän käsityksen nykytilanteesta, jotta oikeat toimenpiteet voidaan tehdä oikeaan aikaan. Tämän avulla järjestelmä pystyy toteuttamaan suuria kustannussäästöjä laitoksessa.
Eqinuor on arvioinut jopa 58 %:n säästön suhteutettuna nykyisiin CUI-kuluihin.
Malux mahdollistaa käyttäjälle tiedon viemisen kentälle tilaluokkaan 1 sekä kaasuryhmään IIC sertifioitujen puhelimien ja tablettien avulla.
Antureiden yksilöidyillä TAG-numeroilla pystytään vuotokohta nopeaasti paikallistamaan.
Yksinkertainen yhteenveto
Antaa mielenrauhaa. Ajoissa saatua tietoa oikean päätöksenteon tukemiseksi.
- Suuret säästöt nykyisiin CUI-kustannuksiin nähden
- 100 % poikkeamien hallinta
- Kosteuden tarkka paikannus
- Luo ymmärrystä kosteuden leviämisestä
- Vältä tarpeetonta eristeiden purkua
- Vältä yllättäviä huoltokatkoja
- Toimi ajoissa valvotuissa olosuhteissa
- Lisääntynyt turvallisuus
- Palaute, jonka avulla parannetaan tietämystä putkien kunnosta.